How safe is your bucket elevator?
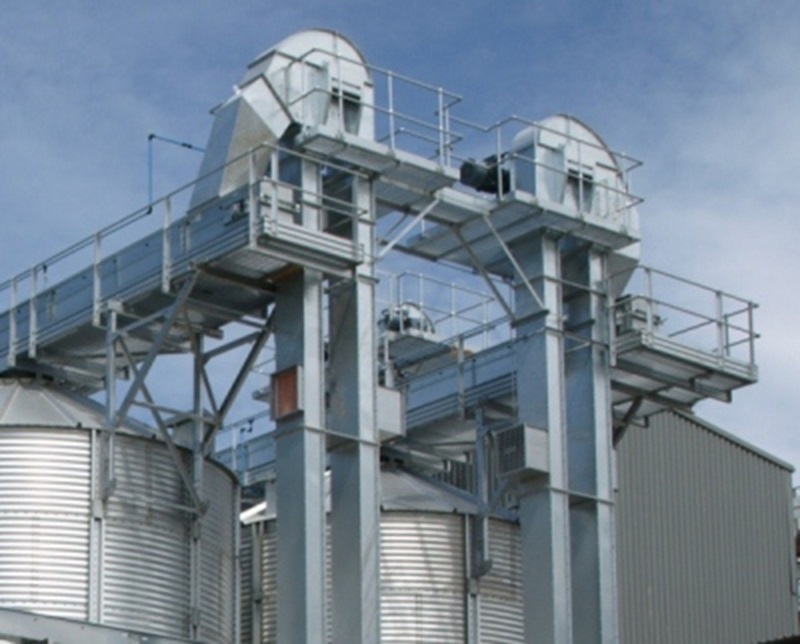
Fires and explosions involving bucket elevators in workplaces can pose serious risks to personnel and plant equipment. Bucket elevators are commonly used to convey bulk materials vertically, and they can be a source of fires and explosions, particularly when handling combustible and explosible materials like grains, coal, or certain chemicals.
This is because when materials are conveyed using bucket elevators, they can release fine particles and dust into the air. Dust accumulation in the bucket elevator or surrounding areas can create a hazardous environment. Furthermore, the movement of materials and buckets within the elevator can generate friction and heat. In some cases, this can lead to overheating, which may act as an ignition source. The movement of materials can also generate static electricity, which can discharge as sparks. These sparks can ignite dust clouds if they contain combustible materials. The Minimum Ignition Energy (MIE) of the material being conveyed will determine the effectiveness of static charges as an effective ignition source. Heat can become trapped within the equipment or dust collectors if not adequately dissipated, increasing the risk of ignition.
Ensuring that effective fire and explosion prevention and mitigation measures are in place is therefore important for life and asset protection. The first step is to install effective dust collection systems and ventilation to capture and remove airborne dust particles. This helps maintain dust concentrations below the explosive limits. Where this is not already installed in an existing site, equipment can be retrofitted to include ventilation and dust collection units.
It is often the case that control of ignition sources will not be a sufficient basis of safety for bucket elevators used to convey combustible materials. Therefore, it is important that you equip the bucket elevator and associated equipment with explosion vents or panels designed to release pressure safely in the event of an explosion. You should also consider using inert gases, such as nitrogen, to reduce the oxygen concentration in the bucket elevator and associated areas, reducing the risk of combustion.
You should ensure that all equipment items, including electrical systems, are properly grounded and bonded to prevent static electricity buildup, which can act as an ignition source. As an additional prevention layer, you should consider installing temperature monitoring devices in critical areas to detect overheating and take corrective actions before ignition occurs. Whilst an effective preventative maintenance programme may seem an obvious measure, you would be surprised how production and work pressures may lead some operators to defer planned maintenance routines. Conducting routine maintenance of bucket elevators and associated equipment ensures that they remain in efficient and safe working order and that potential sources of heat or friction are addressed promptly.
It is often the case that old bucket elevators will not have the required Ex-certification. These may continue to be used provided a Non-Electrical Equipment Ignition Risk Assessment (NEEIRA – also called a MEIRA) has been conducted by a competent person and in line with relevant industry standards such as EN ISO 80079-36:2016. Dunameering Limited has supported many clients in completing NEEIRAs for several pre-ATEX mechanical equipment and can support you in ensuring that you can safely continue to use your bucket elevators in a manner that complies with health and safety regulations.
Preventing fires and explosions in bucket elevators requires a combination of engineering controls, safe operating procedures, and thorough risk assessments. Regular maintenance, inspections, and employee training are essential to maintain a safe working environment in facilities that use bucket elevators for handling combustible materials. Additionally, compliance with industry safety standards and regulations is crucial to minimize the risks associated with these operations.